ILFA invests in the expansion of its PCB lamination capacities
During the LAUFFER Technology Days, ILFA Managing Director Thomas Michels and LAUFFER Managing Director Christof Lauffer announce a close cooperation, which is sealed with a joint letter of intent. The new investment project, which is part of ILFA’s modernisation offensive, is aimed at a highly automated lamination centre that will sustainably support PCB production at ILFA’s Hanover site.
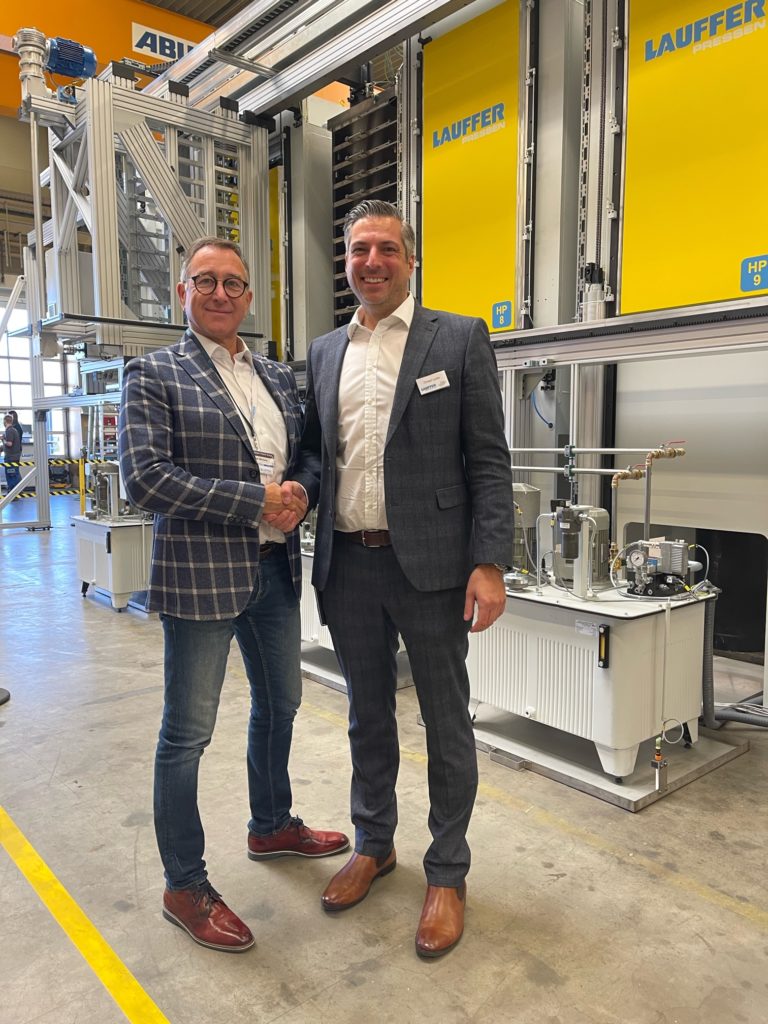
With the planned new investment from LAUFFER, ILFA GmbH will triple its production capacity in the lamination area. At a cost of more than EUR 1.3 million, the laminating centre would be the largest single investment to date in the company’s 43-year history. The modernisation offensive at ILFA provides for total investments in the higher double-digit million range. In addition to increased automation, numerous new acquisitions are currently being made in the areas of OFT (surface technology) and FLT (photo and lacquer technology). These include a new DES line, solder resist developers, micro etching and a new plasma system.
Thomas Michels explains: “On the one hand, we want to grow technologically, but on the other hand, we also want to significantly expand our production capacities. In this way, we will consolidate our position in the market and further establish ourselves in the field of rigid-flex printed circuit boards, RF and power technology as well as in the process-safe processing of the finest structures. We are pleased to have gained LAUFFER as a partner who will support us with its many years of expertise.”
The projected RMV 125/6 LAUFFER lamination centre is characterised above all by a high degree of automation and very high energy efficiency during the lamination process. Thanks to the unique design concept with large storage capacities, which was specially adapted to ILFA’s requirements, the laminating system can be operated fully automatically even during night shifts or so-called ghost shifts. Another innovation is the operation of the system with newly designed heat accumulators for heat recovery during press operation. These enable energy saving effects of up to 30% depending on the operating mode of the entire system. “We are pleased to be able to realise this project together with ILFA. We see this as an important signal for the European PCB industry and especially for the domestic market in Germany,” says Christof Lauffer about the jointly planned project.