Almost EUR 8 million invested in ILFA’s PCB production
Over the past four years, we have invested almost EUR 8 million in our PCB production at our Hanover Anderten site. There have been innovations in almost every department, e.g. new machines and systems, clean room areas and new lighting, air conditioning and automation concepts. Our shutdown a few weeks ago marked an important milestone, as our new LAUFFER pressing centre was installed, which again involved extensive conversion work. This work has now also been completed and our production facility is modern, bright and ergonomic for employees and visitors alike.
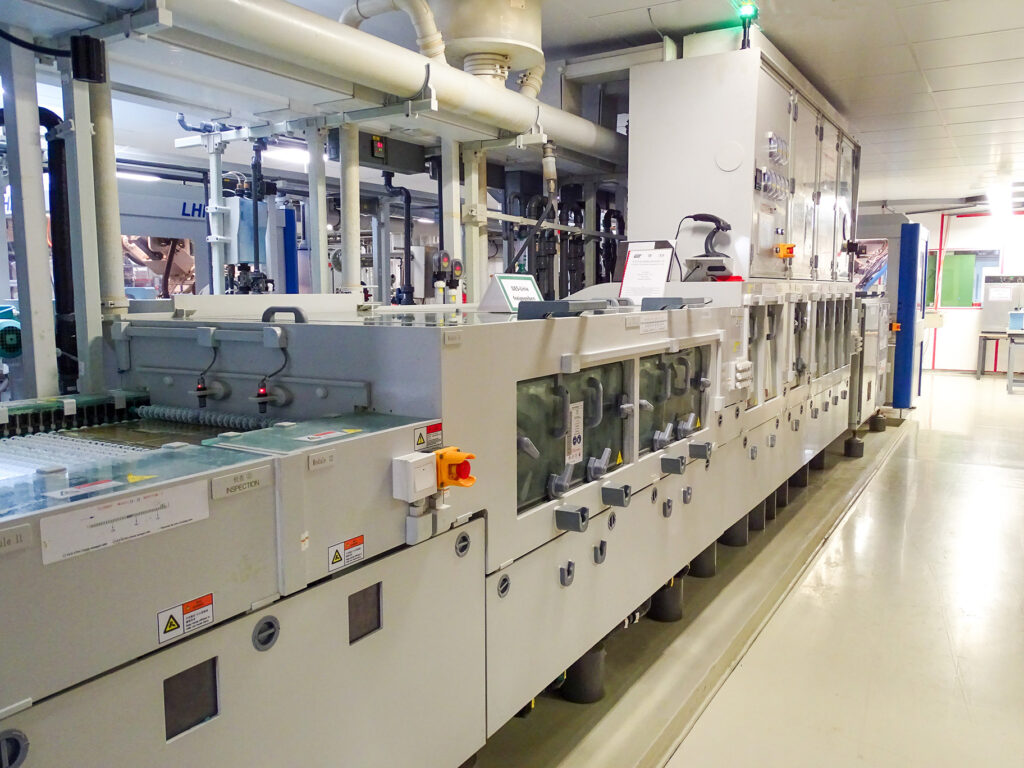
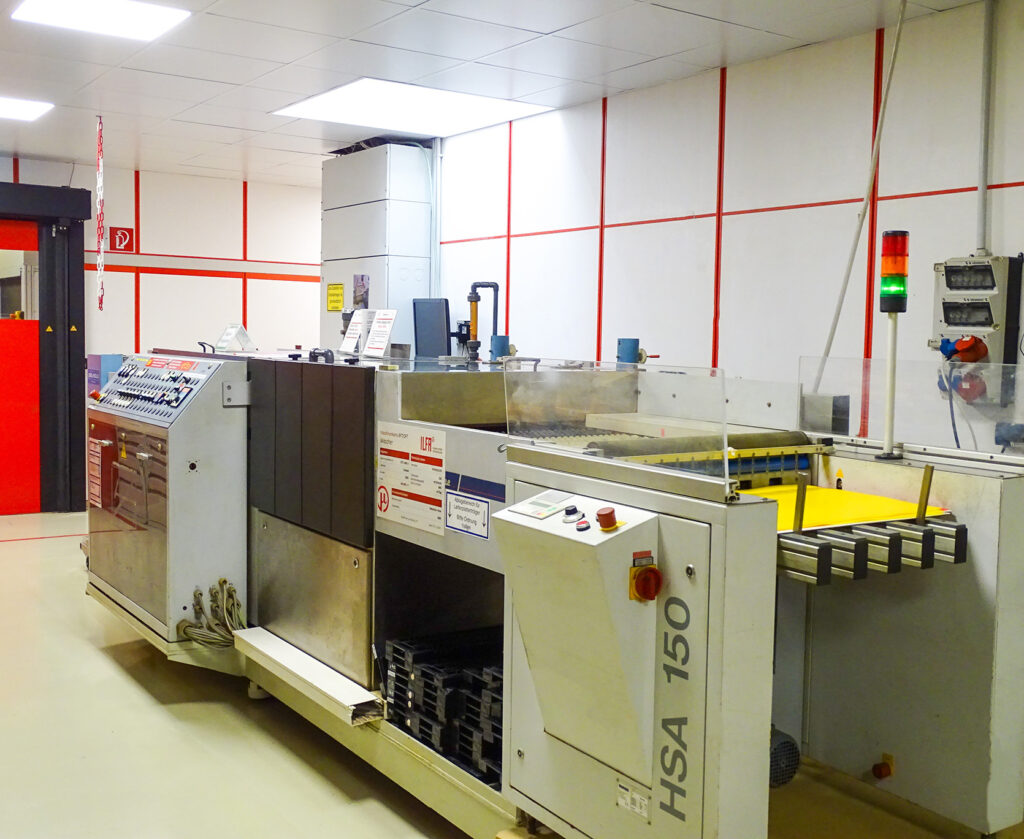
Environmental aspects and a significantly higher degree of automation were also key components of the modernisation work. All of the new machines are naturally more energy-efficient than their predecessors, but we are also increasingly working with heat recovery and have installed a new combined heat and power unit. In terms of automation, we are supported by 16 LHMT handling devices, which, for example, ensure that the machines are loaded and the PCBs are handled correctly. With our new LAUFFER press centre, we can also run ‘ghost shifts’ thanks to sufficient buffer storage.
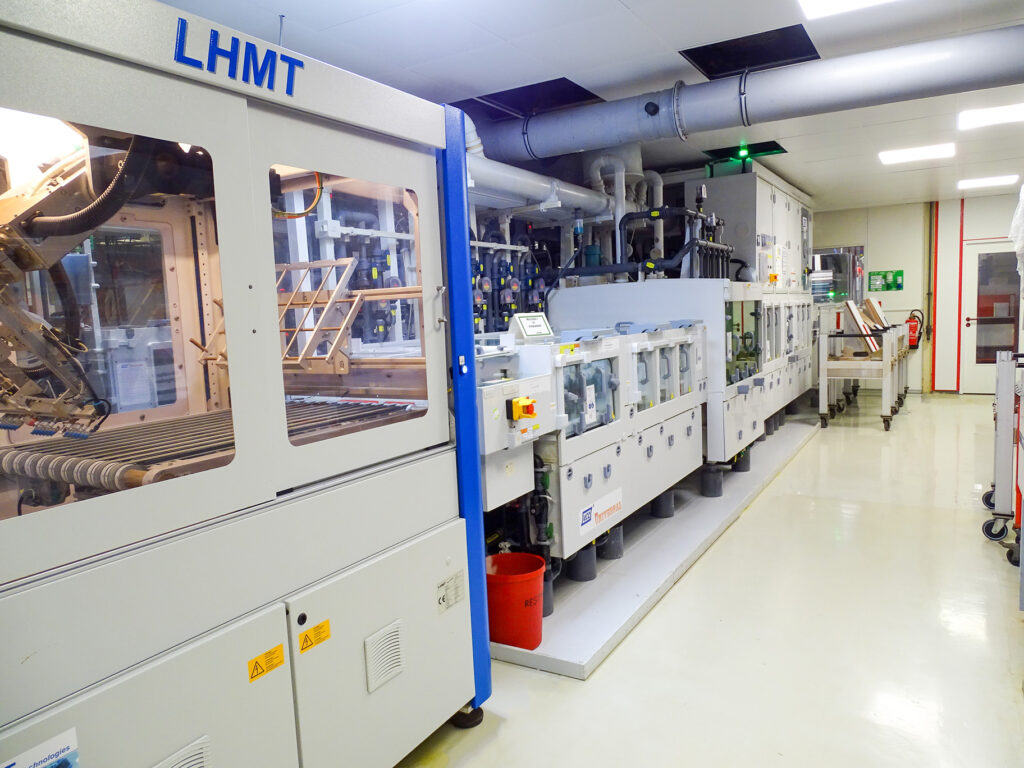
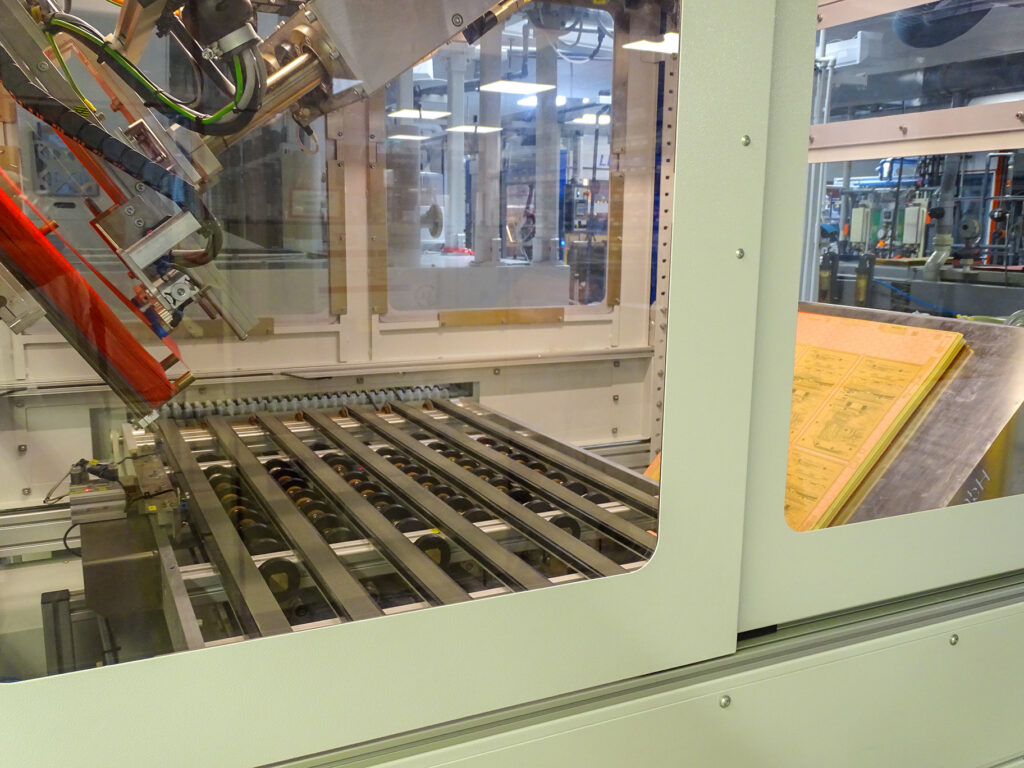
The lighting has been completely converted to LED panels, which provide better lighting but also save valuable energy and do not produce any additional heat. For our new air conditioning concept, a new cooling tower had to be erected on our administration building, among other things, and temperature-critical areas are now kept at a constant temperature level. Our cleanroom areas, where work is carried out under particularly hygienic conditions and access is through airlocks, have also been enlarged.
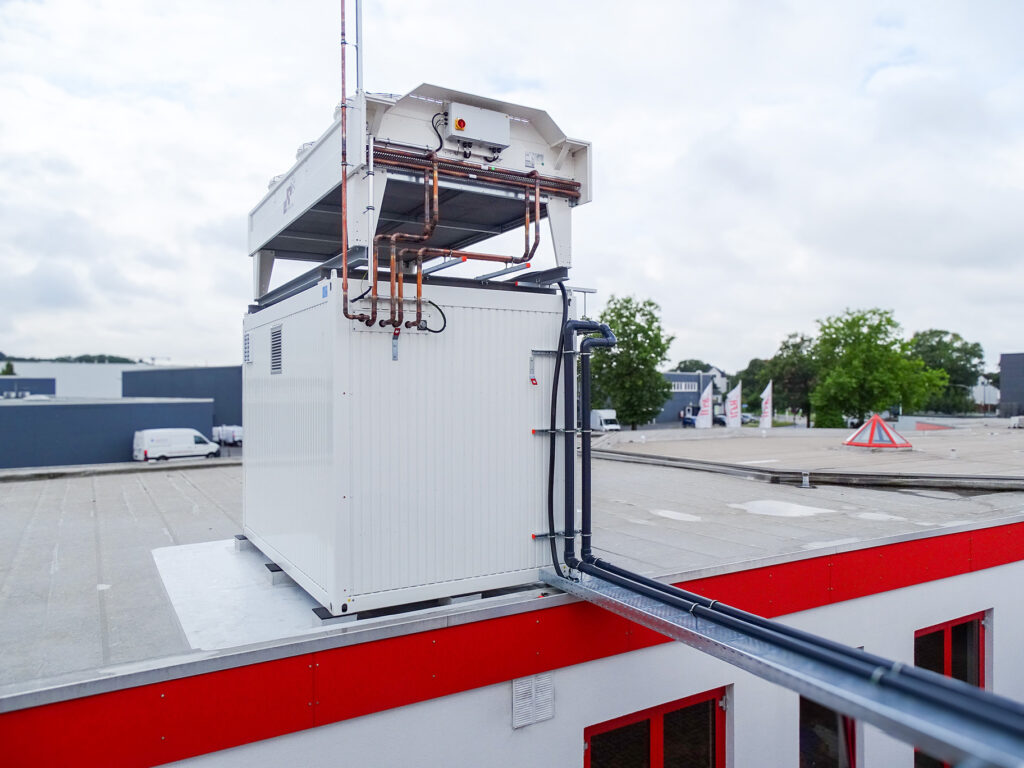
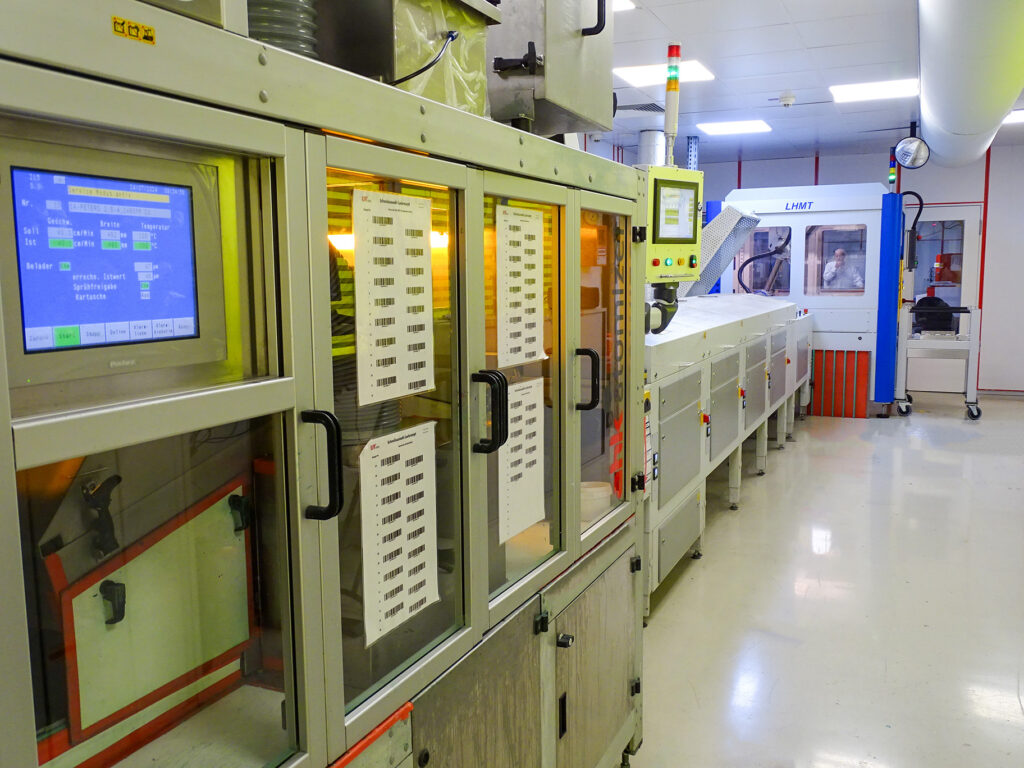
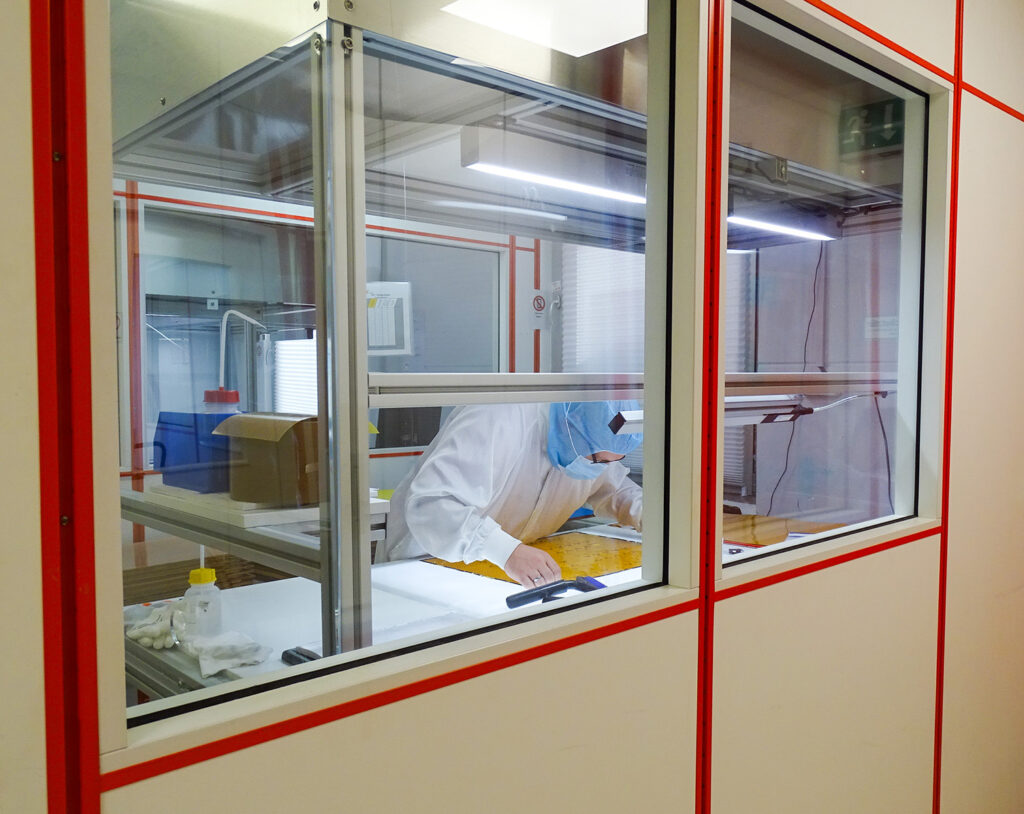
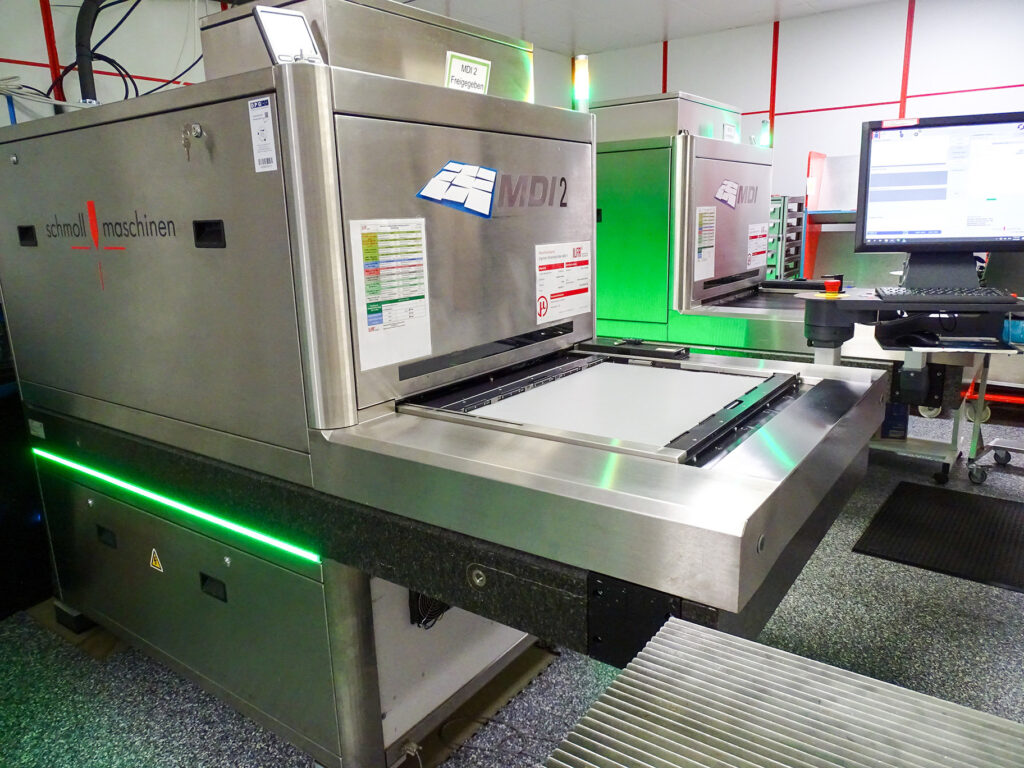
Our new and replacement investments are primarily aimed at technological growth, which enables finer structures or ensures safe use in the high-temperature or high-frequency range, for example. This is our response to the market and to the requirements of our customers, who are increasingly realising more technologically demanding projects.
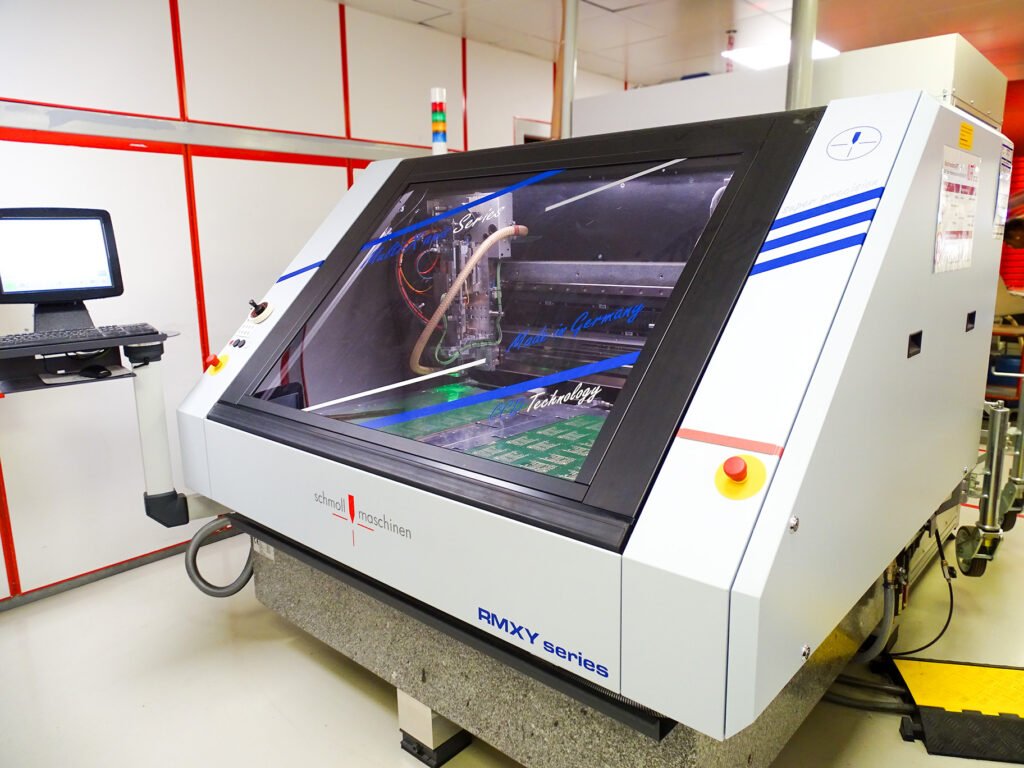
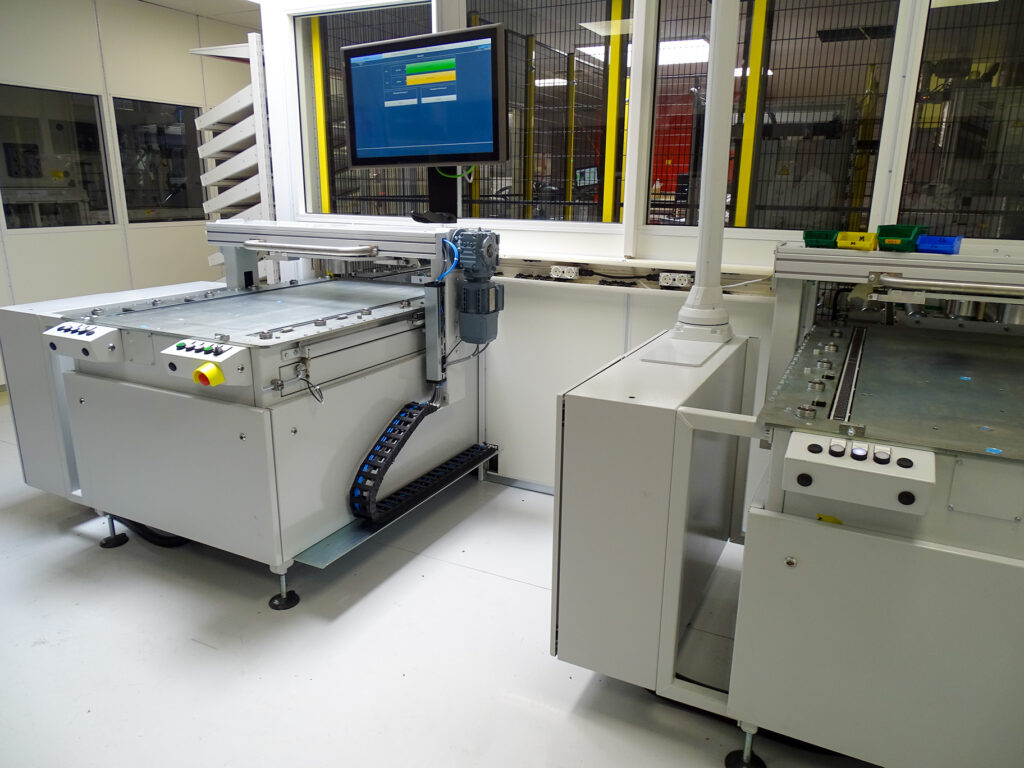
With the extensive innovations, numerous processes within our production also had to be adapted or redefined, which was done across the board. The investments and work have definitely paid off for us. Of course, we are not finished yet, as we are constantly optimising further, we always have new ideas for improvements and still have some very concrete plans where there is still a need for expansion. So you can be curious.