Technologies and processes at ILFA: embedded resistors with OhmegaPly®
Structures on modern printed circuit boards are becoming smaller and smaller, materials are becoming thinner and thinner, and the number of pressings is constantly increasing. This requires certain technologies and processes to be able to meet the requirements of complex PCBs. This time in the spotlight: embedded resistors with OhmegaPly®.
The use of passive electronic components such as SMD resistors is reaching its limits due to advancing miniaturisation, as these cannot always be embedded without problems in PCB production, especially with thin layer structures. Therefore, the processing of resistors integrated into the conductor pattern offers PCB manufacturers an interesting possibility to circumvent this problem. In this process, layers with defined resistance values are integrated into the copper conductor pattern. A well-known product for this process is the OhmegaPly® foil from the company Ohmega Technologies, which consists of a composite of electrolytically deposited nickel phosphide (NiP) on copper, and is available in seven variants from 10 Ohm/square to 377 Ohm/square.
This foil is then pressed onto a dielectric material during PCB production so that the conductor pattern with the resistors can be created in the further process. To do this, the copper is first structured according to the conductor pattern and then the NiP layer is removed with a special chemical. The copper serves as an etch resist so that the NiP layer is later only present under the copper conductor pattern. Finally, in another etching process, the copper is etched away in the areas where the exposed resistors will later be located. With the help of this process, any shapes and resistors can be created according to the customer’s requirements.
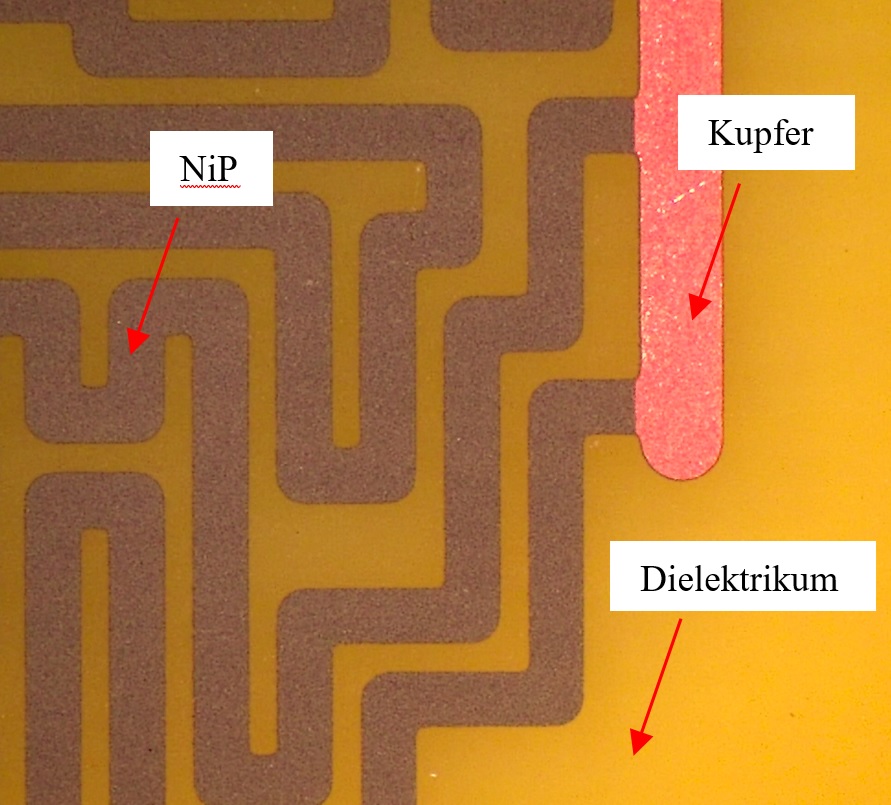
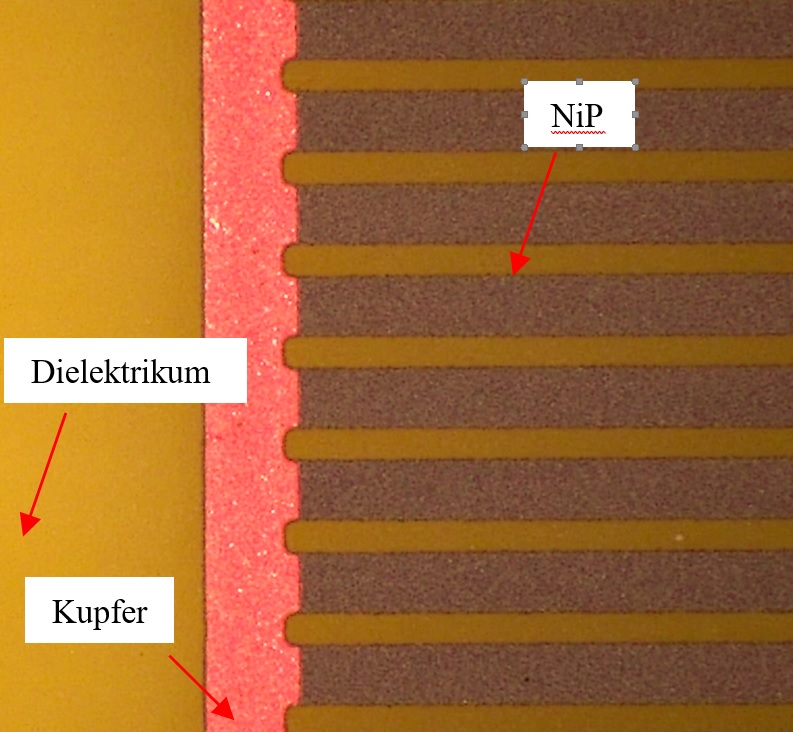
The resistive layer has a thickness of only 1 µm and remains on the surface of the dielectric after etching. The foil is available with different copper treatments to be interesting for high frequency applications, for example.
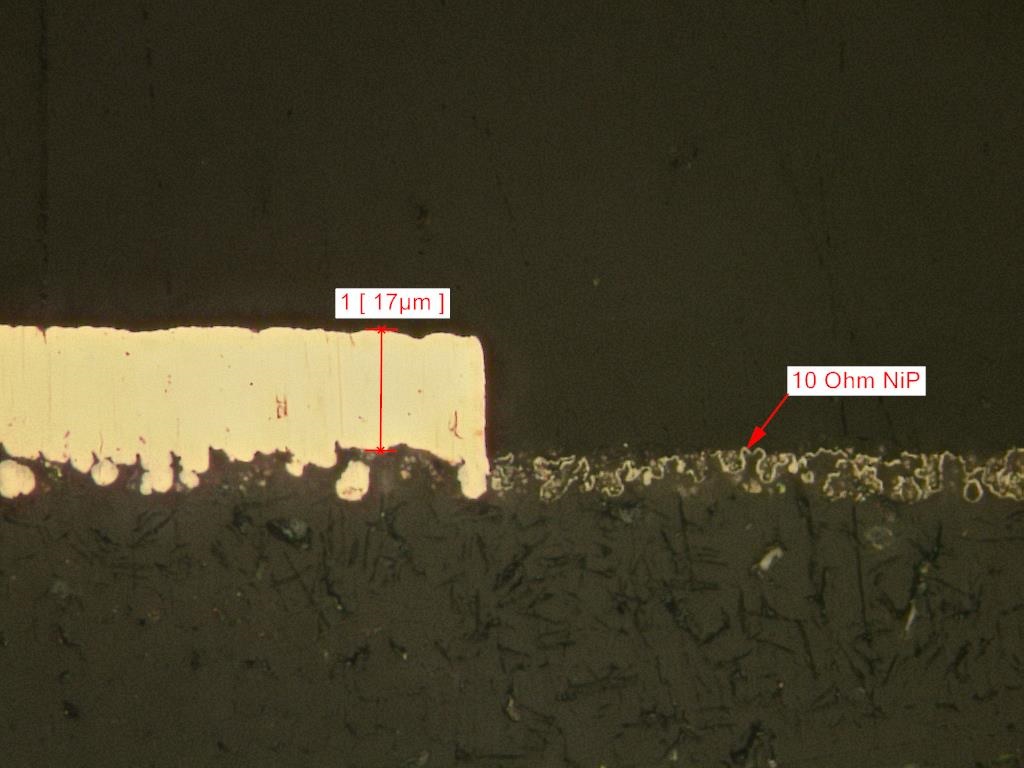
Internal investigations of the process capability show that the fluctuation range of +/- 3% specified by the manufacturer for the 10 Ohm film can be complied with on average.
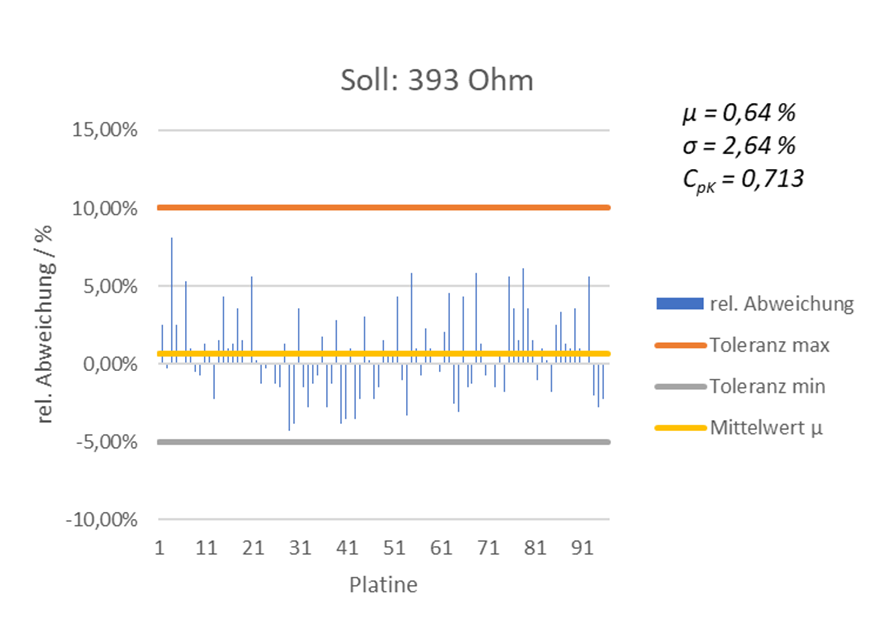
In addition to the film version, Rogers/Arlon also offers PTFE and other base materials with OhmegaPly® film already laminated on. We use OhmegaPly® for a wide range of applications in the aerospace, medical technology and telecommunications sectors. Please contact us about the materials available from us, we will be happy to check your requirements!
Responsible for content: Nikolas Koulouris